Blimp Science
Wingfoot NT
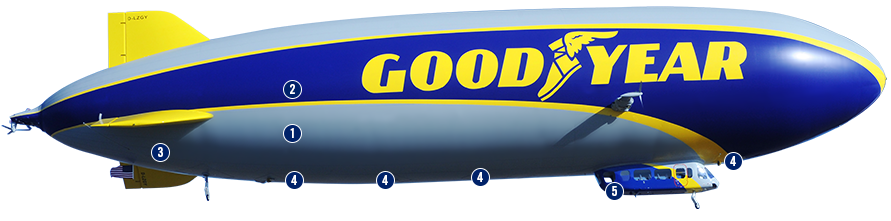
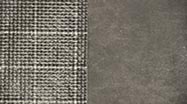
1. Material
The new Wingfoot NT envelope is made from a newer, much lighter compound that is comprised of polyurethane, polyester and a strong, protective film from DuPont™ called Tedlar®.
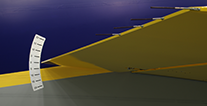
2. Paint
A special Blimp-specific paint formulation is applied using a unique laser-based application process to create the look shown here.
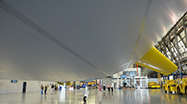
3. Seal
To ensure helium retention, and protect against ultraviolet light, pollution and rupture, the finished, shaped envelope is secured using space-age heat seal technology.
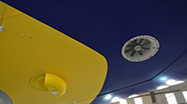
4. Ballonet, Valve & Blower
Ballonet air bags inside the envelope maintain the perfect shape and assist with trim and weight distribution, while the air valve and blower allow the pilot to exhaust and add air when needed.
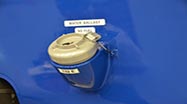
5. Ballast
The new water ballast — which holds up to 185 gallons, or approximately 1,385 pounds, of water — allows the pilot to harmlessly reduce weight while in flight.

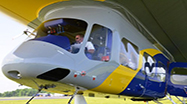
1. Construction
The new Blimp's gondola is made completely of a carbon-fiber composite that weighs in at 2,626 pounds — making it more than 800 pounds lighter than previous models.
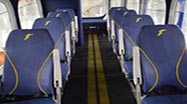
2. Seating & View
With seating for 12 and panoramic windows all around, the new Blimp offers a comfortable ride that provides spectacular aerial views for its passengers.
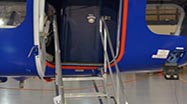
3. Passenger Entry
A wide, comfortable passenger ladder and a large doorway near the rear of the gondola make it easy for passengers to enter, find a seat and exit after their ride.
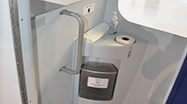
4. Restroom
The new Blimp is the first Goodyear model to have an on-board restroom, which is similar to those found on airplanes, for passengers and crew.
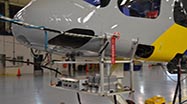
5. Ground Support Rack
When secured to the mast, the equipment on the ground support rack supplies power to run equipment like the blowers and instrument panel, and can be used to start the forward engines if desired.
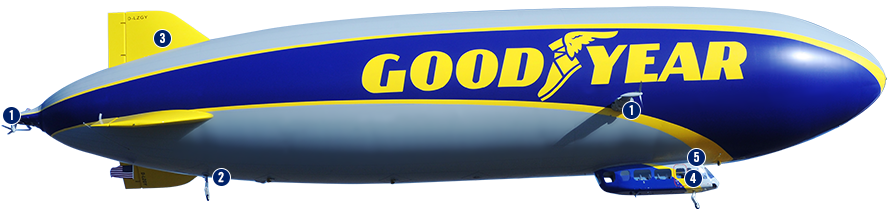
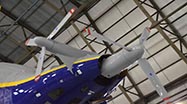
1. Engines
Three four-cylinder, 200-horsepower engines are located on either side of the envelope and at the tail and can propel the airship at speeds of up to 73 miles per hour.
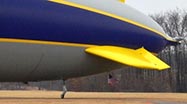
2. Tail Wheel
The new airship’s lower profile brings the tail section closer to the ground and is designed to allow the rear section of the craft to rest on its absorber and tire.
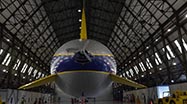
3. Tail Fins
The new Blimp has an "inverted Y" configuration at the tail, and the fin control surfaces operate in tandem as "ruddervators" for directional navigation using fly-by-wire electrical control.
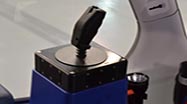
4. Side Stick Controls
Located next to both left and right seats, these electrical controls are used to steer the Blimp left and right, up and down, using the main three tail fin control surfaces.
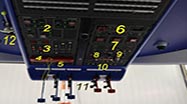
5. Overhead Panel
Individual circuit breakers allow pilots or mechanics to isolate and control any piece of equipment including the engine, fuel system, air and helium, radio, exterior lighting and more.
How it's Made
Assembly of Wingfoot One began in March 2013 at Goodyear's Wingfoot Lake hangar. An international team of engineers and technicians from Goodyear and Germany's ZLT Zeppelin Luftschifftechnik worked side by side to complete the build project. Parts such as the tail fins and gondola were built in Germany and shipped to the U.S. for assembly. The balloon-like body of the airship – the “envelope” – is made of polyester with an innovative film from DuPont™ called Tedlar®, surrounding a semi-rigid internal structure, which differentiates this airship from previous Goodyear blimps.
The timelapse video shows the process of the Wingfoot NT from beginning to completion. Enjoy!
Airship Types
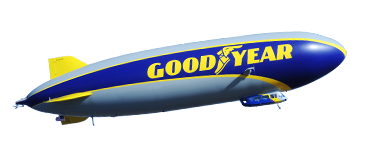
Semi-rigid airships, such as the new Goodyear Blimp, have an internal rigid lower or upper frame and a pressurized envelope. The Wingfoot NT has an upper frame. Previously, the most famous of this type was NORGE, the airship which General Umberto Nobile used on his attempt to reach the North Pole. The last semi-rigid airship Goodyear built before the Wingfoot NT was the RS1 for the United States Army in 1926!
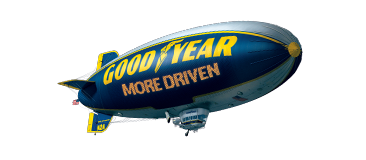
These airships have no internal frame. The internal pressure of the lifting gas (non-flammable helium) and air-filled ballonet bags maintain the shape of the envelope. The only solid structural parts are external: the passenger car, the nose battens (hollow aluminum tubes at the nose of the Blimp) and the tail fins.
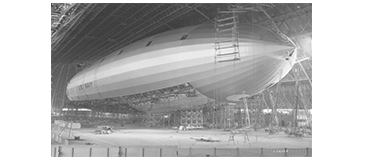
Rigid airships have an internal frame. The Zeppelins and the U.S.S. Akron and Macon were famous rigid airships. The rigid structure, traditionally an aluminum alloy called duralumin, holds up the form of the airship, rather than internal pressure. In general, rigid airships are only efficient when longer than 120 Meters (360 feet) because a good weight to volume ratio is (or was) only achievable for large airships. For a small airship the solid frame would have been too heavy.